E-Connect
Imagine a scenario on your production line where your turning machine is running a batch of parts from an expensive alloy bar stock. Each part requires 5” of material, leaving you with 4” of stock remaining. Instead of wasting this costly piece of metal, the E-Connect solution allows the turning machine and barfeed to communicate and figure out how to make a good part from the remaining material without additional operator time.
E-Connect is a cutting-edge solution developed by LNS that maximizes productivity and efficiency. It enables real-time information sharing between your turning machine and LNS barfeed, allowing them to analyze material usage and adjust part programs on the fly. This means you can reduce material waste and labor costs while making your production process more efficient.
E-Connect helps you save time, labor, and material, making your production line more efficient and profitable.
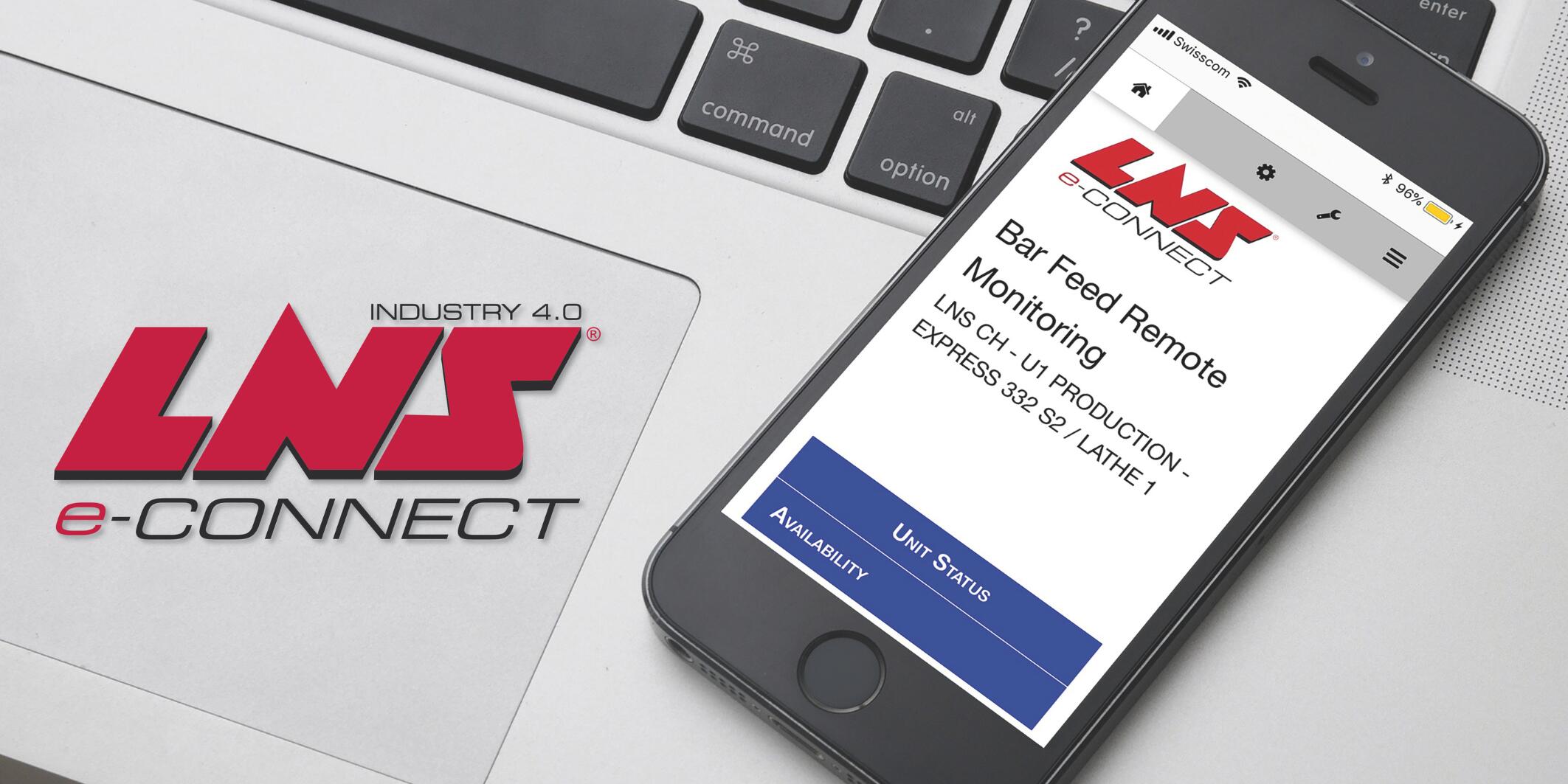